The heart of any belt filter press operation is the belt filter press cloth. This specialized fabric plays a critical role in separating solids from liquids, influencing factors like cake dryness, filtrate quality, and overall process efficiency. Choosing the right belt filter press cloth is essential for maximizing your equipment’s performance and minimizing downtime.
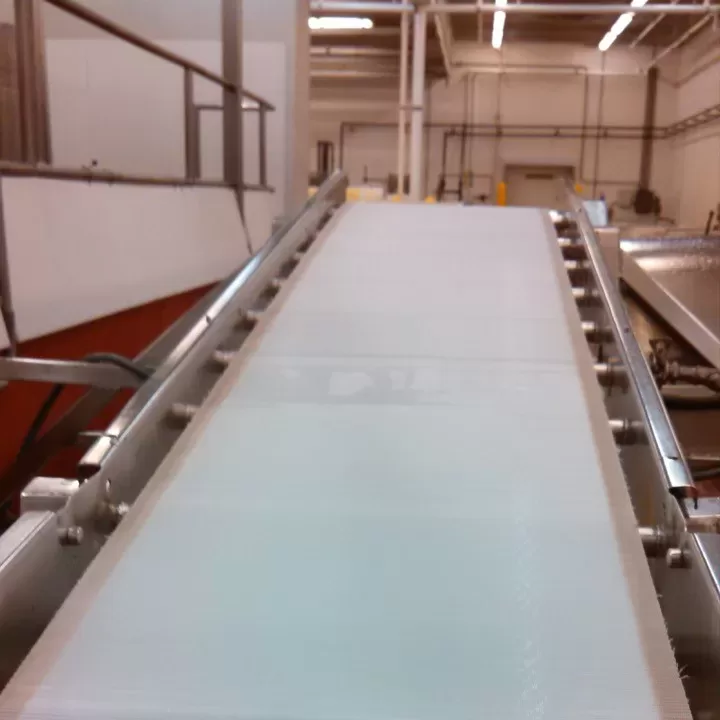
Understanding Belt Filter Press Cloth Functions
Belt filter press cloths perform two primary functions within the dewatering process:
- Solid-Liquid Separation: The fabric acts as a barrier, allowing filtrate (liquid) to pass through while retaining solids on the belt. Pore size and weave patterns significantly impact separation efficiency.
- Cake Formation and Release: The cloth supports the formation of a solid cake during the high-pressure zone. Its characteristics influence cake thickness, moisture content, and ease of release from the belt for optimal throughput.
Key Considerations for Selecting Belt Filter Press Cloth
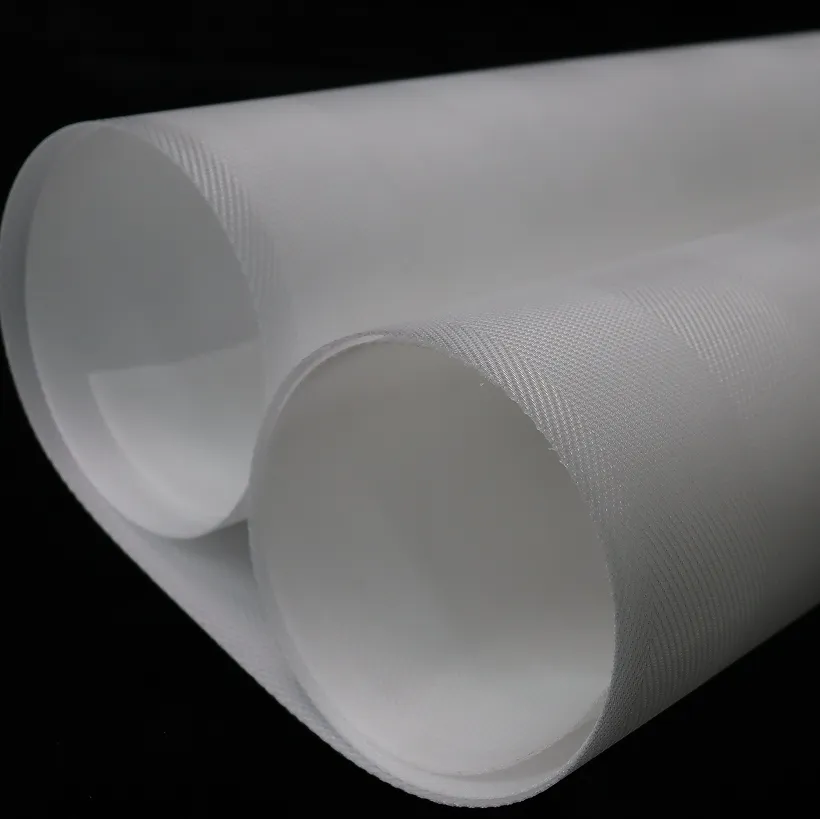
Several factors influence the selection of the best belt filter press cloth for your application. Here are the crucial aspects to consider:
- Feed Material Characteristics: Particle size, shape, and surface properties of the solids in your slurry significantly impact cloth selection. For instance, finer particles require tighter weave patterns.
- Filtrate Clarity Requirements: The desired level of filtrate clarity will influence the pore size of the chosen cloth. Tighter pores ensure clearer filtrate but may also reduce flow rate.
- Cake Discharge Properties: The cloth’s surface properties and release characteristics can affect how easily the cake detaches from the belt, impacting overall processing speed.
- Chemical Compatibility: The cloth material must be compatible with the process chemicals used to ensure optimal performance and lifespan.
- Temperature Resistance: The operating temperature range of your belt filter press needs to match the cloth’s thermal tolerance.
- Cost-Effectiveness: Finding the right balance between cloth performance, durability, and cost is crucial for long-term operational efficiency.
Types of Belt Filter Press Cloth
Belt filter press cloths are typically made from woven synthetic fibers, with the most common materials being:
- Polyester (PET): Offers a good balance of strength, chemical resistance, and affordability. Ideal for various applications.
- Polypropylene (PP): High chemical resistance and excellent for abrasive slurries. May not be suitable for high temperatures.
- Nylon (PA): Offers high strength and elasticity, making it suitable for demanding applications. Can be more expensive than other options.
Weave Patterns for Belt Filter Press Cloth
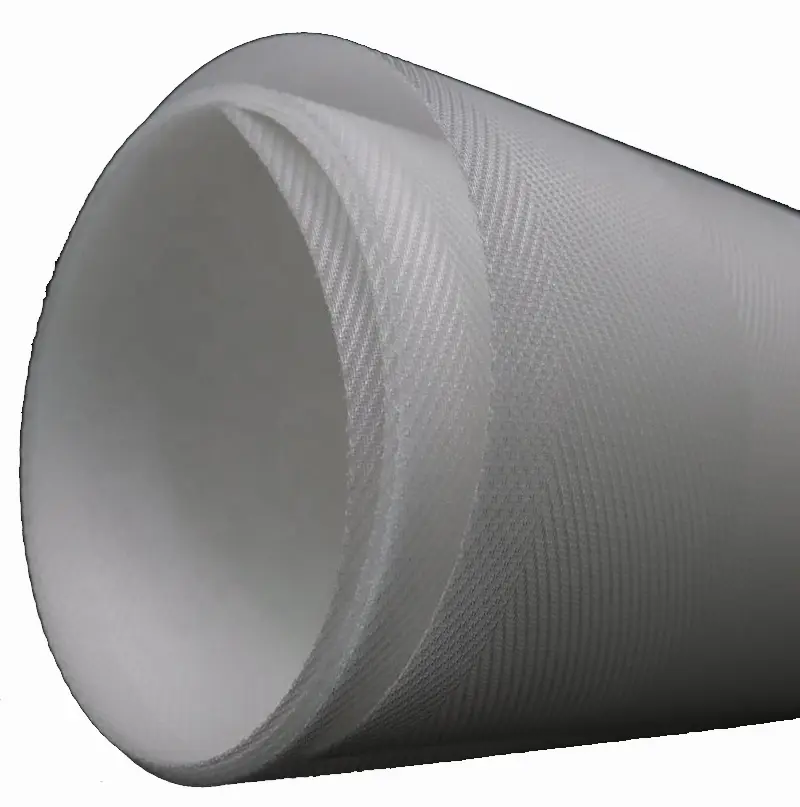
The weave pattern of the cloth significantly impacts its performance. Here are the most common types:
- Monofilament: Single strands of yarn woven into an open mesh. Offers high permeability for excellent filtrate flow rates but may not achieve the highest solids capture for finer particles.
- Multifilament: Strands of multiple fibers woven together. Provides a balance between permeability and solids capture, making it a versatile choice.
- Twill Weave: Offers a denser structure compared to monofilament, suitable for capturing finer solids while maintaining good flow rates.
Specifications of Our Belt Filter Press Cloth
Type | Woven Filter |
Use | Liquid Filter |
Material | PP |
Thickness | 1.2-2.3mm |
Weight | 1.6Kg/m² |
Color | Orange, White, Blue |
Finalization setting | Twice heat-setting |
Specifications | Customized as your demand |
Air permeability | 9m³/m²*min |
Weft tensile strength | 150kg/m |
Warp tensile strength | 255kg/m |
Filtration accuracy | 10-300um |
Weaving method | Three layers of twill |
Optimizing Belt Filter Press Cloth Performance
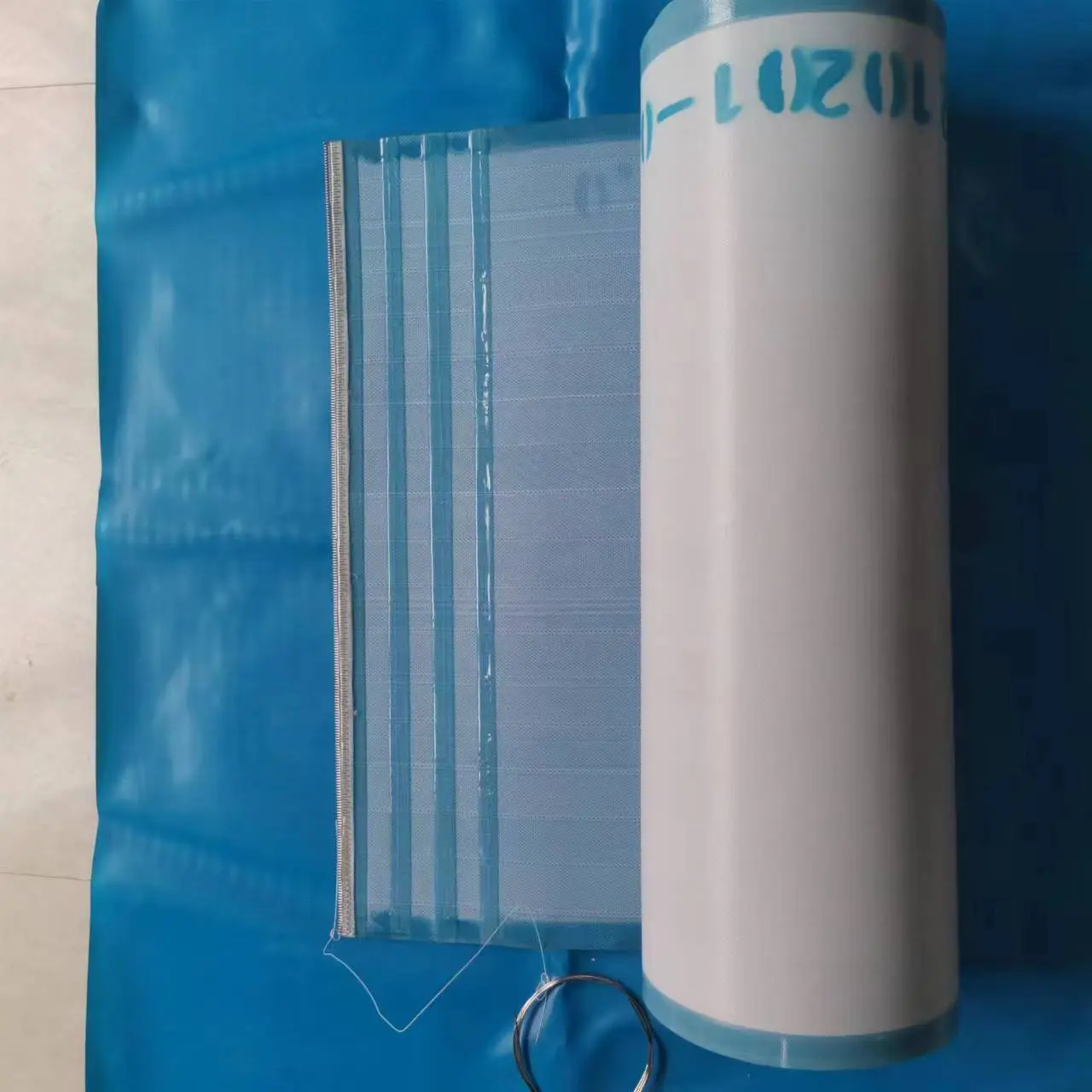
- Proper Cloth Selection: Choosing the right cloth for your specific application is crucial for optimal performance. Consult with a belt filter press cloth manufacturer or supplier for expert recommendations.
- Effective Cleaning and Maintenance: Regular cleaning and maintenance of the cloth are essential to prevent blinding (pore clogging) and ensure optimal filtrate quality and cake discharge.
- Monitoring and Replacement: Monitor cloth performance regularly and replace it when signs of wear, blinding, or reduced efficiency become evident.
By following these guidelines and utilizing a high-quality belt filter press cloth, you can ensure your belt filter press operates at peak efficiency, maximizing throughput, filtrate quality, and overall process profitability.
For expert advice and high-performance belt filter press cloth solutions, contact ChinaFilter today!